Choosing the Right Bandsaw Blade
Bandsaw blades differ in size, length, material, and tooth configuration so choosing the right blade is vital to get the best results, depending on the material and shapes you are cutting.
General blades can be good for most sawing, but if you are cutting more complex materials and shapes the right blade will stop you from wasting blades or material. Ideally, you will have different blades for your bandsaw if you cut different types of material. It’s always wise to have more than one bandsaw blade as a back-up in case the one you’re using is damaged.
Our guide sets out the most important factors you need to consider when choosing your blade.
It’s worth beginning with the terminology used to describe different parts of a bandsaw blade. They are:
Tooth Face. This is the surface of the tooth.
Tooth Pitch. Also known as the distance between the tip of one tooth and that of the nearest tooth.
Gullet. This is the curved area you find at the bottom of the tooth.
TPI. This stands for teeth per inch and is the measurement between the gullets.
Tooth Rake Angle. The angle referred to is that of the tooth face perpendicular to the direction in which the saw is cutting.
Blade Width. This is the measurement you find between the end of a tooth and the back of the band.
Blade Thickness. This refers to how much the saw measures between either side of the blade.
Blade Set. When you bend the teeth right or left there is a certain amount of clearance from the back of the blade through the cut. This is known as the 'set.'
Blade Back. As the name suggests, this is the opposite side of the blade to the teeth.
Kerf. This is the material that is discarded when the blade cuts through the item.
CHOOSING THE RIGHT BANDSAW BLADE SIZE
Bandsaw blades are circular in shape when ready for use and can be welded to custom sizes by specialist blade suppliers like Saws UK. The easiest way to find the right size blade for your bandsaw is to refer to your bandsaw’s instruction manual or to measure an existing blade.
The blade length, thickness and width is usually determined by your saw’s wheel size. Smaller bandsaws need thinner blades to prevent the welds breaking. Larger saws can usually handle thicker and wider blades with no issues.
Bandsaw Blade Length
The length of the blade is effectively the circumference – the length of the blade if you imaging it rolled flat before it has been welded together. Measuring from one end to the other gives you the required length.
However, it’s quite tricky to measure the length: one common trick is to mark the blade, lay out a measuring tape, and then roll the bandsaw from the mark until it reaches the mark again.
If you don’t have a manual or blade, and there are no markings on your machine, you can follow these steps to determine your blade length:
• Set the pulleys or wheels to working position
• Measure the distance between the centres (C) on the drive wheels
• Measure the radius of the upper and lower drive wheels. (R Up & R Lo)
• The blade length is calculated as follows: (R Up X 3.146) + (R Lo X 3.146) + (2 X C)
The Thickness / Width of your Bandsaw Blade
The width of the blade is measured from the tip of the tooth of the blade to the flat part of the bottom of the blade.
The thickness of the blade you need depends on your bandsaw size, what you are cutting and how smooth the cut needs to be.
If you have a small, three-wheeled bandsaw, you will need a thin blade as it’s the only one that has enough flexibility to fit around the wheels. Larger three-wheeled bandsaws can use thicker blades.
For re-sawing or cut-off sawing, using your bandsaw’s maximum blade width is advised as this keeps cuts nice and straight. Thicker blades can withstand more strain and speed, but they can also break more easily. Thinner blades are better for lighter work and advised if you are cutting curves or contours. As a rule, the narrower the width, the tighter the cut radius and the better a blade will be for curved cuts.
Bandsaw Blade Width & Minimum Radius
The list below shows the correlation between the blade width and the minimum radius it will cut.
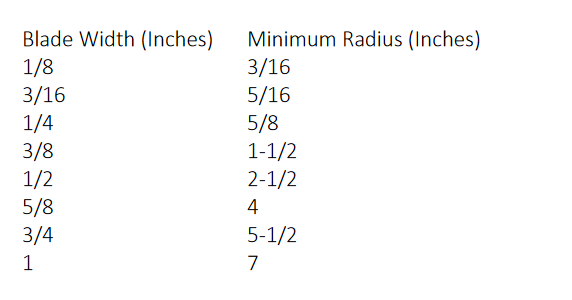
Saws UK’s highly experienced team will be able to help you find the right length of blade if you are still having difficulty
.
HOW MANY TEETH PER INCH?
The tooth pitch refers to the number of teeth per inch (tpi) on the blade. At Saws UK, we estimate that nearly 50% of bandsaw machines are using the wrong tooth pitch for the section of work being cut.
As a rule, at least three teeth should be engaged in the material you are cutting, with a maximum of 18.
Blades with fewer teeth will cut faster, with a better clearance but with a slightly rougher finish. These blades are more suited to deeper stock, so they are good for resawing.
A blade in the 6 to 8 TPI range is considered a good general-purpose blade. Blades that are 14tpi and above are generally used for cutting thin stock, for cutting plastics, and non-ferrous metals. Blades for plastic or metal cutting usually have more teeth. Blades with a higher tpi will cut slower and produce a smoother cut and finer finish.
View our chart to determine the minimum thickness material by tooth pitch:
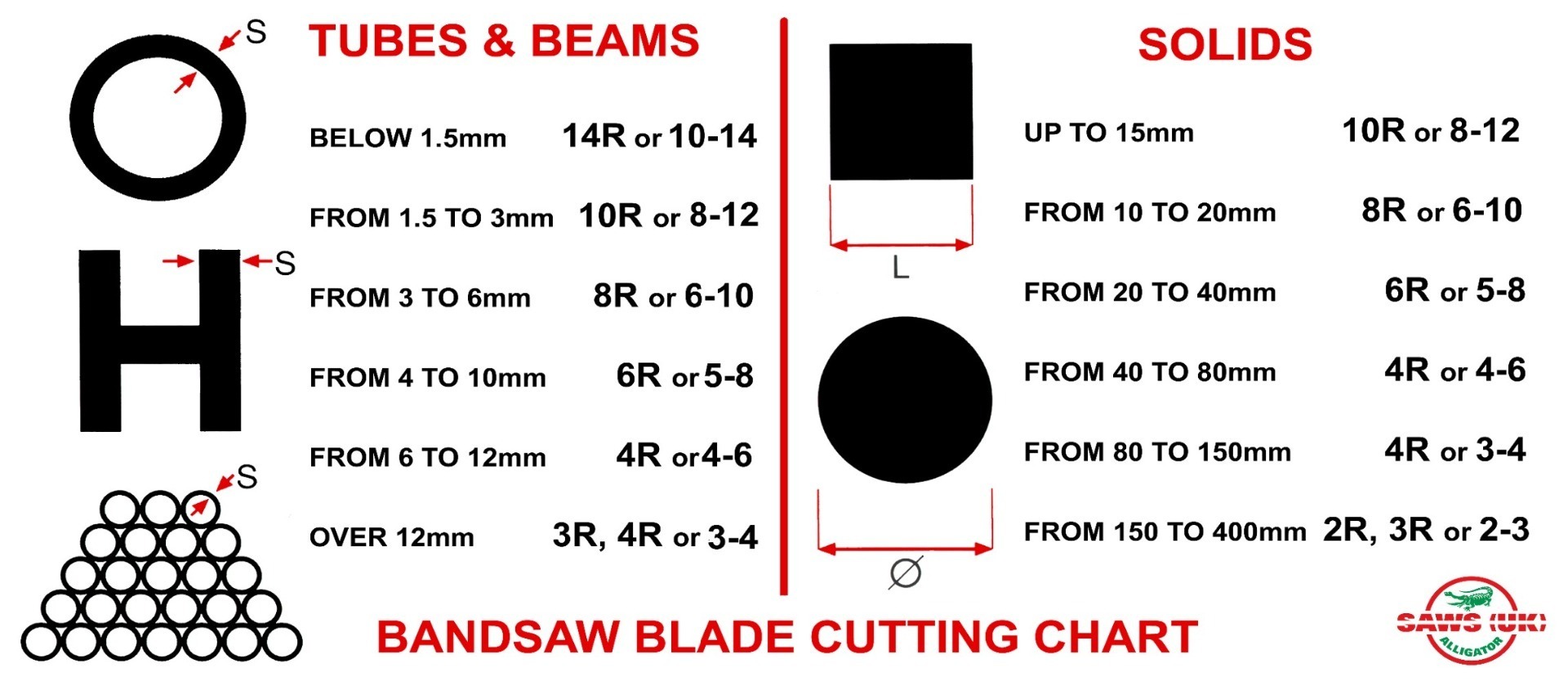
TYPES OF TEETH ON A BANDSAW BLADE
Another important consideration is the type of tooth you need.
Options include:
Regular Tooth: this is when the teeth are straight; the blades generally have deep gullets between each tooth. These are used for general metal cutting and smooth woodworking cuts
Hook Tooth: a hook tooth bandsaw blade has deep gullets (longer teeth) and they are widely spaced with a 10 degree rake angle which makes them ideal for coarse, fast cuts. These blades can be used to cut non-ferrous alloys, woods, and plastics, and are a good option when you need a deep cut
Skip tooth: on these blades, the teeth are widely spaced with a 0-degree rake angle. These blades are great for woodwork and for soft, non-ferrous materials that might otherwise clog
Variable tooth: these blades have alternating sets of different sized teeth, providing a fast, smooth cut. This type of tooth reduces vibrations, which is important when cutting in and out of holes and slots. The variable-tooth blade is an all-purpose blade used for woodworking and contouring.
Types of Tooth Sets
Sets refer to the arrangement of the teeth on the blades:
A raker tooth set has one tooth going to the left, one to the right, followed by a straight, or unset, tooth, which is known as a raker. This is a good blade for wood and for coarse metals
A wavy tooth set has groups of teeth set left and right, separated by unset raker teeth. Wavy set blades are made primarily with the small teeth and are used for cutting thinner metal sections, tubes, pipes, thin sheets and small shapes.
An alternate tooth set has one tooth going left, one going right, and so on, but there are no raker teeth.
Surface Feet Per Minute (SFM) or Surface Meters Per Minute (SMM)
The Surface Feet/Meter Per Minute allows you to set the correct speed for the material you are cutting, which is specific to your bandsaw. This information should listed in your bandsaw manufacturer’s guide – contact our helpful team if you need more help with this on 0800 521 292.
TYPES OF BANDSAW BLADES
General Purpose Bandsaw Blades
General purpose bandsaw blades are perfect for cutting softer materials like wood, plastics, foams, paper and non-ferrous metals like steel and stainless steel. They are also ideal for cutting bundles, tubes and solids.
Our general-purpose blades are a good choice if you do a lot of cutting, but if you need to radius cut, veneer cut, cut thick stock or green stock, or are working with more complicated materials, then picking a specialist blade is recommended.
We offer two main types of general purpose blades, and a huge range of different brands:
• Carbon Steel General Purpose Blades: these are general purpose bi-metal blades for steel, stainless steel, bundles, tubes and solids, and they are perfect for cutting softer materials like wood, plastics, foams, paper and non-ferrous metals. We have a huge selection of tooth pitches and widths - we offer all sizes and tooth pitches in thicknesses of 0.025' and thicker.
• Bi-Metal General Purpose Blades: Our premium M42, bi-metal bandsaw blades are perfect for general use as well as production-cutting of hardwood and metal solids like stainless steel. This blade is the perfect choice if you are looking for a high quality, general-purpose blade for your bandsaw, with precision cutting and an extended blade life. They are more durable than most blades on the market, due to their hardened teeth made from M42 cobalt steel. They also have enhanced heat and wear resistance – making our bandsaw blades much more cost-effective long-term. They are designed for production and general-purpose sawing, and are ideal for cutting metals, solids, bundles, pipes, profiles and castings.
Features include:
Variable angle geometry depending on the tooth pitch, which reduces vibration and noise
Special set
Shock resistant design
Tooth capped for additional safety
Improved productivity and performance, with fast cutting ability and clean cuts
M42 Bi-Metal Bandsaw Blades - Metal or Wood (last longer)
Made from triple tempered M42 cobalt high-speed steel with hardened teeth, these blades will last on average around 5 - 10 times longer than other blades. Another advantage of the M42 blades is that they will cut through the occasional nail without damaging the blade or causing the blade to go blunt. M42 blades are especially popular for cutting re-claimed timber and hardwoods where the extra blade life means that these blades are very economical to run.
S42 Bi-Metal Bandsaw Blades – Structural
The S42 blades are extra set, shock-resistant, M42 carbon steel bandsaw blades for structural sections and beams, together with bundles of heavy wall tubes and SHS, when stronger teeth and better clearance are required. They can withstand high heat and are more durable than most blades on the market, due to their hardened teeth made from M42 cobalt steel, making our bandsaw blades much more cost-effective long-term.
Variable angle geometry
Special set
Strengthened tooth design
Withstands high heat
Shock resistant design, reducing vibration, broken blades, pinching and stripped teeth
Ideal for:
Channel, bundles and angle iron
I Beams, H Beams
Structural steel sections
Box section or round tube
Bi-Metal Blades - Ground Tooth
Developed for production-cutting of hard metal solids, this blade cuts with high precision and has an extended blade life, and is perfect for cutting metal and difficult materials.
A smooth surface finish is ensured not only by the latest ground tooth technology, but also by the precise set. Special combination tooth design and sharp cutting edges allow easy penetration while the M42 tooth tips withstand high heat. This bi-metal blade is the perfect choice for quality bandsawing of alloyed and stainless steels and difficult materials.
They are more durable than most blades on the market, due to the ground tooth design, making them sharper and more uniform in height.
Ideal for:
Metal cutting
Hard metal solids
Difficult materials
Carbide Grit Bandsaw Blades
Our carbide grit blades are used to cut abrasive materials between 45 and 65 HRC and for cutting hardened steels, fibreglass, graphite, composites, cables, cast iron, car tyres, low density ceramics and a wide variety of difficult materials.
We sell these bandsaw blades in segmented form for larger work pieces, and with a continuous grit edge for cutting finer or thinner sections.
These hard-wearing bandsaw blades provide an optimal solution for heavy-duty cutting. We offer a wide range of widths, all welded to order.
Carbide Tipped Bandsaw Blades
Carbide Tipped blades have been developed for cutting hardened or abrasive metals and faster cutting. Standard Bi-Metal blades can cut up to RC (Rockwell C Scale) 39, whereas Carbide can cut up to RC 55 (or slightly higher in certain circumstances). Carbide is associated with high durability and high heat resistance. Due to this carbide tipped blades and carbide blades are better alternative to bi-metal blades due to its higher RC rating, economy and production time saving.
Carbide is best suited for use in solid materials because the continuous cut faces less vibration than when cutting structural or thin wall tubing.
Carbide blades can be classified into several basic categories:
General Purpose: recommended for cutting operations that frequently change the materials being cut. Carbide blades are developed to be versatile, working on a wide range of materials and reducing the need to change blades.
Hard-to-Cut Metals: optimised for aerospace alloys containing high amounts of nickel, such as stainless steel and Inconel.
Extreme Performance: coated carbide blades – applying a thin film coating to the tooth edge of a blade helps transfer the heat from the cutting edge of the blade to the chips. This protection enables the blade to stay cool, cut faster and provide much longer blade life.
Specific: blades engineered with specific cutting operations in mind.
For more information- or if you’re not sure of the right blade, our expert team can give you a chart to ensure you choose the right one for your bandsaw machine. Just call us on 01892 663398 or email [email protected] for guidance.
Alternatively, you can buy a selection of bandsaw blades online or order custom length bandsaw blades from our helpful team.
Tagged as: Bandsaw Blades
Share this post: